COGM: Master Cost Of Goods Manufactured (2024 Guide)
Ever wondered how a company truly knows its profit margins? Understanding the Cost of Goods Manufactured (COGM) is absolutely critical; it's the financial bedrock upon which profitability assessments are made in the manufacturing world. Without it, you're essentially flying blind.
COGM isn't just some obscure accounting term; it's a vital metric that reflects the total expenses a company incurs to complete the production of its goods during a specific period. Think of it as the financial DNA of a product, tracing its journey from raw materials to a finished, ready-to-sell item. Understanding and accurately calculating COGM allows businesses to make informed decisions regarding pricing, cost control, and overall operational efficiency. In essence, mastering COGM is about mastering the financial health of your manufacturing operations. It's a far deeper dive than simply looking at revenue; it's about understanding the intricacies of production costs and how they impact your bottom line.
Attribute | Details |
---|---|
Definition | Cost of Goods Manufactured (COGM) represents the total production costs incurred by a company during a specific accounting period to manufacture its products. |
Components | Direct materials, direct labor, and manufacturing overhead. |
Formula | Beginning Work-in-Process (WIP) Inventory + Total Manufacturing Costs - Ending Work-in-Process (WIP) Inventory |
Significance | Helps in determining profitability, pricing strategies, cost control, and financial reporting accuracy. |
Distinction from COGS | COGM represents the cost of goods manufactured, while Cost of Goods Sold (COGS) represents the cost of goods sold. COGS includes finished goods inventory adjustments. |
Industry Relevance | Crucial for businesses in the manufacturing sector to effectively manage their production costs and financial performance. |
Link | AccountingTools |
The Cost of Goods Manufactured (COGM) equation is deceptively simple at first glance, but its accurate calculation requires a keen understanding of its components. The fundamental formula involves adding the total manufacturing costs – encompassing direct materials, direct labor, and factory overhead – to the beginning work in process inventory, and then subtracting the ending work in process inventory. Each element plays a crucial role, and errors in any one area can significantly skew the final COGM figure.
- Caroline Kennedys Illness Unlocking The Mysteries Of Mental Health
- Unveiling The Enduring Love Story Of Eddie Vedder And Jill Mccormick
Let's break down each component:
- Direct Materials: These are the raw materials that directly become part of the finished product. Think of the lumber used to build a table, the fabric used to sew a shirt, or the silicon wafers used to manufacture computer chips. Tracking direct materials involves carefully monitoring the cost of these materials from the moment they enter your inventory until they are consumed in the production process. Accurate inventory management is crucial here.
- Direct Labor: This refers to the wages and benefits paid to the workers who are directly involved in the manufacturing process. These are the individuals who are actively transforming raw materials into finished goods. Examples include assembly line workers, machine operators, and welders. Accurately tracking direct labor costs requires meticulous timekeeping and allocation of labor hours to specific production activities.
- Factory Overhead: This is the catch-all category that encompasses all other manufacturing costs that are not directly attributable to direct materials or direct labor. It's a broad category that includes everything from factory rent and utilities to depreciation on manufacturing equipment and the salaries of factory supervisors. Allocating factory overhead can be complex, as these costs often benefit multiple production activities. Common allocation methods include using machine hours, direct labor hours, or a percentage of direct labor costs.
- Beginning Work in Process (WIP) Inventory: This represents the value of partially completed goods that are still in the production process at the beginning of the accounting period. It's essentially the carryover from the previous period's production activities. Accurate tracking of beginning WIP inventory is essential for ensuring that all production costs are captured in the COGM calculation.
- Ending Work in Process (WIP) Inventory: This represents the value of partially completed goods that are still in the production process at the end of the accounting period. It's the inventory that will be carried over to the next period's production activities. Accurately valuing ending WIP inventory is crucial for avoiding double-counting costs in the COGM calculation.
Now, let's consider the difference between Cost of Goods Manufactured (COGM) and Cost of Goods Sold (COGS). While the terms are often used interchangeably, they represent distinct concepts. COGM, as we've discussed, focuses on the manufacturing costs, encompassing everything required to produce the goods. COGS, on the other hand, focuses on the selling costs. It represents the cost of the goods that a company actually sold during a specific period. The key difference lies in the treatment of finished goods inventory.
Think of it this way: a company may manufacture a large quantity of goods during a period, but it may not sell all of those goods during that same period. The cost of all those manufactured goods is captured in COGM. However, only the cost of the goods that were actually sold is captured in COGS. The remaining goods are held in finished goods inventory and will be included in COGS when they are eventually sold. The relationship between COGM and COGS can be summarized as follows:
- Unveiling The Genius Discoveries And Insights From Henry Omaga Diaz
- Unveiling The Unseen Inside The Lives Of Jeff Foxworthys Kids
Beginning Finished Goods Inventory + COGM - Ending Finished Goods Inventory = COGS
Understanding this distinction is crucial for accurately interpreting a company's financial performance. COGM provides insights into the efficiency of the manufacturing process, while COGS provides insights into the profitability of sales.
Beyond the theoretical understanding, let's examine the practical implications of COGM. Imagine you're managing a furniture manufacturing company. You need to decide whether to invest in new, more efficient equipment. A thorough COGM analysis can help you determine whether the investment will result in lower production costs and ultimately improve profitability. By comparing the COGM before and after the investment, you can quantify the cost savings and make a data-driven decision.
Furthermore, COGM plays a crucial role in pricing strategies. Understanding the true cost of manufacturing your products allows you to set prices that are competitive yet profitable. If you underestimate your COGM, you risk underpricing your products and eroding your profit margins. Conversely, if you overestimate your COGM, you risk overpricing your products and losing sales to competitors.
Moreover, COGM is essential for accurate financial reporting. It's a key component of the income statement and is used to calculate gross profit. Accurate COGM figures ensure that your financial statements provide a true and fair representation of your company's financial performance. This is particularly important for publicly traded companies that are required to comply with strict financial reporting regulations.
However, calculating COGM can present several challenges. Accurately tracking direct materials costs can be difficult, especially when dealing with volatile commodity prices or complex supply chains. Allocating factory overhead can also be challenging, as these costs often benefit multiple production activities. Moreover, valuing work in process inventory requires careful judgment and can be subjective.
To overcome these challenges, companies should implement robust accounting systems and processes. This includes:
- Implementing a robust inventory management system to track the flow of raw materials and work in process.
- Using timekeeping systems to accurately track direct labor hours.
- Developing a clear and consistent method for allocating factory overhead.
- Establishing clear procedures for valuing work in process inventory.
- Regularly reviewing and auditing COGM calculations to ensure accuracy.
Let's explore some real-world examples of how COGM is used in different industries. In the automotive industry, COGM is used to track the cost of manufacturing vehicles, from the raw materials used in the chassis to the labor required to assemble the engine. Automakers use COGM to identify areas where they can reduce production costs and improve profitability. They might negotiate better prices with suppliers, invest in automation to reduce labor costs, or streamline their manufacturing processes to reduce waste.
In the food and beverage industry, COGM is used to track the cost of producing food and beverage products, from the cost of ingredients to the cost of packaging. Food and beverage companies use COGM to determine the profitability of different products and to make decisions about pricing, product development, and marketing. They might adjust their recipes to use less expensive ingredients, optimize their packaging to reduce material costs, or focus their marketing efforts on their most profitable products.
In the technology industry, COGM is used to track the cost of manufacturing electronic devices, from the cost of components to the cost of assembly. Technology companies use COGM to determine the profitability of different devices and to make decisions about product design, manufacturing outsourcing, and pricing. They might redesign their products to use fewer components, outsource their manufacturing to lower-cost countries, or adjust their pricing to remain competitive in the market.
Now, let's delve into the crucial components that make up the Cost of Goods Manufactured (COGM). These elements are the building blocks that, when meticulously tracked and calculated, provide a comprehensive view of a company's manufacturing expenses.
Direct Materials: As previously mentioned, direct materials are the raw materials that become an integral part of the finished product. The accuracy of direct materials costing begins with a robust inventory management system. This system should track the quantity and cost of each raw material from the moment it enters the warehouse to the moment it is used in production. Techniques like First-In, First-Out (FIFO) or Weighted Average cost methods are often employed to determine the cost of materials consumed during production. Furthermore, managing supplier relationships and negotiating favorable pricing agreements are crucial for controlling direct material costs. Companies can also explore value engineering techniques to identify opportunities to use less expensive materials without compromising product quality.
Direct Labor: Direct labor encompasses the wages, salaries, and benefits paid to employees who are directly involved in the manufacturing process. Accurately tracking direct labor costs requires a detailed understanding of the time spent by each employee on specific production activities. Timekeeping systems, such as punch clocks or electronic time tracking software, are commonly used to record labor hours. It's also important to consider factors like overtime pay, payroll taxes, and fringe benefits when calculating total direct labor costs. Furthermore, investing in employee training and development can improve productivity and reduce labor costs per unit.
Manufacturing Overhead: Manufacturing overhead represents all other manufacturing costs that are not directly attributable to direct materials or direct labor. This category includes a wide range of expenses, such as factory rent, utilities, depreciation on manufacturing equipment, factory supplies, and the salaries of factory supervisors. Allocating manufacturing overhead to specific products or production activities can be complex. Common allocation methods include using machine hours, direct labor hours, or a percentage of direct labor costs. The choice of allocation method should be based on the specific characteristics of the manufacturing process. For example, if a company relies heavily on automated equipment, machine hours may be the most appropriate allocation method. Regular analysis of overhead costs can help identify areas where costs can be reduced or controlled.
Work-in-Process (WIP) Inventory: Work-in-process (WIP) inventory represents partially completed goods that are still in the production process. Accurately valuing WIP inventory requires careful consideration of the stage of completion of each product and the costs incurred to date. Companies often use a percentage of completion method to estimate the value of WIP inventory. This method involves estimating the percentage of work that has been completed on each product and then multiplying that percentage by the total estimated cost to complete the product. Regular physical inventory counts are essential for verifying the accuracy of WIP inventory records.
To further illustrate the calculation of COGM, let's consider a simple example. Imagine a company that manufactures wooden chairs. At the beginning of the year, the company had $10,000 in work-in-process inventory. During the year, the company incurred the following manufacturing costs:
- Direct materials: $50,000
- Direct labor: $30,000
- Factory overhead: $20,000
At the end of the year, the company had $5,000 in work-in-process inventory. Using the COGM formula, we can calculate the company's COGM as follows:
COGM = Beginning WIP Inventory + Total Manufacturing Costs - Ending WIP Inventory
COGM = $10,000 + ($50,000 + $30,000 + $20,000) - $5,000
COGM = $105,000
Therefore, the company's Cost of Goods Manufactured for the year is $105,000.
In conclusion, understanding the Cost of Goods Manufactured (COGM) is essential for any manufacturing business. It's a crucial metric for managing profitability, making informed decisions, and ensuring accurate financial reporting. By carefully tracking the components of COGM and implementing robust accounting systems and processes, companies can gain valuable insights into their manufacturing costs and improve their overall financial performance. COGM is not just an accounting exercise; it's a strategic tool that can help manufacturers thrive in a competitive marketplace.
General Motors (GM), a global automotive giant, exemplifies the critical role of COGM in managing its complex manufacturing operations. GM produces a wide range of vehicles under brands like Buick, Cadillac, GMC, and Chevrolet. Understanding and controlling the cost of goods manufactured is paramount for GM to maintain profitability in a highly competitive industry.
For GM, COGM encompasses the costs of raw materials like steel, aluminum, and plastic; the direct labor costs of assembly line workers; and the vast array of manufacturing overhead expenses associated with running its sprawling factories. Accurately calculating and managing COGM allows GM to make informed decisions about pricing, production efficiency, and investment in new technologies.
For instance, GM's decision to invest in electric vehicle (EV) production is heavily influenced by COGM considerations. The company needs to carefully analyze the COGM of EVs compared to traditional gasoline-powered vehicles to determine the potential profitability of this new technology. This analysis involves considering the cost of battery components, the labor required to assemble EVs, and the manufacturing overhead associated with producing EVs on a large scale.
Furthermore, GM uses COGM to monitor the performance of its different manufacturing plants. By comparing the COGM of similar vehicles produced at different plants, GM can identify best practices and areas for improvement. This helps the company to optimize its manufacturing processes and reduce costs across its global operations.
In addition to internal decision-making, COGM is also essential for GM's financial reporting. Accurate COGM figures are required for the company's income statement and are used to calculate gross profit. This information is crucial for investors and other stakeholders who rely on GM's financial statements to assess its performance.
The recent collaboration between TWG Motorsports and GM to develop a Cadillac Formula 1 team further underscores the importance of COGM in the automotive industry. The cost of designing, building, and racing a Formula 1 car is enormous, and understanding COGM is crucial for managing the financial risks associated with this venture. GM needs to carefully track the costs of research and development, manufacturing, logistics, and personnel to ensure that the Formula 1 team is financially sustainable.
The principles of COGM extend beyond the automotive industry and are applicable to any manufacturing business, regardless of its size or sector. Whether you're producing automobiles, food and beverage products, or electronic devices, understanding and managing COGM is essential for success. It's the key to unlocking profitability, improving efficiency, and making informed decisions that drive growth.
One area often overlooked within COGM is the impact of waste and inefficiency. Lean manufacturing principles can be instrumental in minimizing waste and streamlining processes, directly contributing to lower COGM. This involves identifying and eliminating non-value-added activities, optimizing inventory levels, and improving production flow. By embracing lean manufacturing, companies can significantly reduce their COGM and improve their overall competitiveness.
Another critical aspect of COGM management is the use of technology. Enterprise Resource Planning (ERP) systems can automate many of the tasks involved in tracking and calculating COGM, providing real-time visibility into manufacturing costs. These systems can also help companies to improve their inventory management, track labor hours, and allocate overhead costs more accurately. Investing in the right technology can significantly enhance a company's ability to manage its COGM effectively.
Moreover, companies should regularly review and update their COGM calculations to reflect changes in their manufacturing processes, raw material costs, and labor rates. This ensures that the COGM figures remain accurate and relevant. It's also important to benchmark COGM against industry peers to identify areas where the company can improve its performance.
In today's dynamic business environment, where competition is fierce and margins are often tight, understanding and managing COGM is more critical than ever. It's not just about knowing the cost of producing your goods; it's about using that knowledge to make strategic decisions that drive profitability and growth. By embracing a data-driven approach to COGM management, manufacturers can gain a significant competitive advantage.
The concept of "biaya produksi barang" (cost of production of goods) as it's understood in Indonesian business practices, aligns closely with the principles of COGM. The Indonesian term encompasses the same core elements: bahan baku (raw materials), tenaga kerja (labor), and biaya overhead pabrik (factory overhead). Understanding these parallels allows businesses operating in diverse global markets to apply the fundamental principles of COGM effectively.
Ultimately, COGM is a powerful tool that empowers manufacturers to take control of their costs, improve their efficiency, and drive sustainable growth. It's a journey of continuous improvement, where ongoing analysis, optimization, and investment in technology lead to long-term success. By mastering COGM, manufacturing businesses can position themselves for a brighter future in an increasingly competitive world.
The principles of COGM aren't confined to large corporations like General Motors. Small and medium-sized enterprises (SMEs) in the manufacturing sector can also benefit significantly from understanding and applying these concepts. In fact, for SMEs, effective COGM management can be even more crucial, as they often operate with tighter margins and fewer resources than larger companies.
For example, a small furniture manufacturer can use COGM to determine the true cost of producing its chairs and tables. This allows the manufacturer to set competitive prices that are still profitable. By carefully tracking the cost of lumber, labor, and overhead, the manufacturer can identify areas where costs can be reduced. Perhaps the manufacturer can negotiate better prices with its lumber supplier, invest in more efficient woodworking equipment, or streamline its production process to reduce labor hours.
Similarly, a small food processing company can use COGM to track the cost of producing its sauces and condiments. This allows the company to determine the profitability of its different products and to make decisions about pricing, product development, and marketing. The company can analyze the cost of ingredients, packaging, and labor to identify opportunities for cost reduction. Perhaps the company can switch to less expensive ingredients, optimize its packaging to reduce material costs, or improve its production process to reduce waste.
Even for very small manufacturing businesses, such as artisans or craftspeople who produce handmade goods, understanding COGM can be valuable. While they may not have formal accounting systems, they can still track their costs and use that information to make better decisions about pricing and product development. By understanding the true cost of their materials, labor, and overhead, they can ensure that they are charging enough to make a profit and to sustain their business.
The key for SMEs is to start simple and gradually build their COGM management capabilities over time. They don't need to implement complex accounting systems overnight. They can start by tracking their direct materials costs and labor hours. As they become more comfortable with these concepts, they can gradually add more sophisticated methods for allocating overhead costs and valuing work-in-process inventory.
The availability of affordable accounting software and online resources has made it easier than ever for SMEs to manage their COGM effectively. These tools can automate many of the tasks involved in tracking and calculating COGM, freeing up time for business owners to focus on other aspects of their operations. By embracing technology and adopting a data-driven approach to COGM management, SMEs can improve their profitability, efficiency, and competitiveness.
Furthermore, SMEs can benefit from seeking advice from accountants or consultants who specialize in manufacturing accounting. These professionals can provide guidance on setting up appropriate accounting systems, tracking costs effectively, and interpreting COGM data. They can also help SMEs to identify opportunities for cost reduction and process improvement.
In conclusion, COGM is not just for big corporations. It's a valuable tool for all manufacturing businesses, regardless of their size. By understanding and managing their COGM effectively, SMEs can improve their profitability, efficiency, and competitiveness, and position themselves for long-term success.
Beyond the practical applications within manufacturing firms, understanding COGM extends its relevance into the realms of financial modeling and investment banking. Financial analysts and investment bankers leverage COGM data to gain a deeper understanding of a manufacturing company's efficiency, profitability, and overall financial health.
In financial modeling, COGM serves as a critical input for projecting future earnings and cash flows. Analysts use historical COGM data to estimate future production costs and to assess the impact of various scenarios on a company's profitability. For example, analysts might model the impact of changes in raw material prices, labor rates, or production volume on COGM and ultimately on the company's bottom line.
Investment bankers rely on COGM data to value manufacturing companies for mergers and acquisitions (M&A) transactions. A thorough understanding of COGM allows investment bankers to assess the target company's profitability, efficiency, and potential for future growth. They can also use COGM data to identify opportunities for cost savings and operational improvements that could increase the value of the company.
Furthermore, COGM is used in credit analysis to assess the creditworthiness of manufacturing companies. Lenders use COGM data to evaluate a company's ability to generate sufficient cash flow to repay its debts. A high COGM relative to sales may indicate that a company is struggling to control its production costs and may be at higher risk of default.
In the context of initial public offerings (IPOs), COGM data is scrutinized by potential investors to assess the company's business model and its potential for future profitability. Investors want to see that the company has a clear understanding of its production costs and that it is taking steps to manage those costs effectively.
Moreover, COGM is used in industry analysis to compare the performance of different manufacturing companies within the same sector. By comparing COGM data across companies, analysts can identify best practices and benchmarks for efficiency and profitability. This information can be valuable for investors who are looking to identify the most attractive investment opportunities within a particular industry.
The insights derived from COGM analysis extend beyond the traditional financial metrics. They provide a window into the operational efficiency, supply chain management, and production processes of a manufacturing company. This holistic view is invaluable for making informed investment decisions and for advising companies on strategies to improve their financial performance.
In conclusion, COGM is not just an internal accounting metric. It's a powerful tool that is used by financial professionals to assess the performance, value, and creditworthiness of manufacturing companies. Understanding COGM is essential for anyone who wants to make informed decisions in the world of finance and investment.
As the manufacturing landscape continues to evolve with the advent of new technologies like artificial intelligence (AI), machine learning (ML), and advanced robotics, the importance of COGM will only increase. These technologies have the potential to significantly impact manufacturing costs, and companies that can effectively manage their COGM will be best positioned to capitalize on these opportunities.
AI and ML can be used to optimize production processes, reduce waste, and improve quality control. For example, AI-powered systems can analyze data from sensors and cameras to identify defects in real-time, allowing manufacturers to take corrective action before those defects lead to costly rework or scrap. ML algorithms can also be used to predict demand, optimize inventory levels, and improve supply chain management.
Advanced robotics can automate repetitive tasks, reduce labor costs, and improve productivity. Robots can be used to perform tasks such as welding, painting, and assembly, freeing up human workers to focus on more complex and value-added activities. The use of robotics can also improve safety and reduce the risk of injuries in the workplace.
These technologies can have a significant impact on COGM. By reducing waste, improving quality, and increasing productivity, they can help manufacturers to lower their production costs and improve their profitability. However, these technologies also require significant investments in hardware, software, and training. Companies need to carefully analyze the costs and benefits of these investments and to ensure that they are aligned with their overall business strategy.
Furthermore, the adoption of these technologies will require manufacturers to develop new skills and capabilities. Workers will need to be trained to operate and maintain these advanced systems. Companies will also need to develop new data analytics capabilities to extract insights from the vast amounts of data generated by these technologies.
The companies that can successfully integrate these new technologies into their manufacturing processes and effectively manage their COGM will be the winners in the future. They will be able to produce higher-quality goods at lower costs, allowing them to compete more effectively in the global marketplace.
In conclusion, the future of manufacturing is being shaped by new technologies that have the potential to transform production processes and significantly impact COGM. Companies that embrace these technologies and develop the skills and capabilities to manage them effectively will be well-positioned for success in the years to come. The understanding and effective management of COGM will remain a cornerstone of success in the evolving manufacturing landscape.
- Angela Eguavoen Unraveling The Essence Of Identity Culture And Social Justice
- Unveiling The Secrets Of Lindsey Lohan Botox Discoveries And Insights
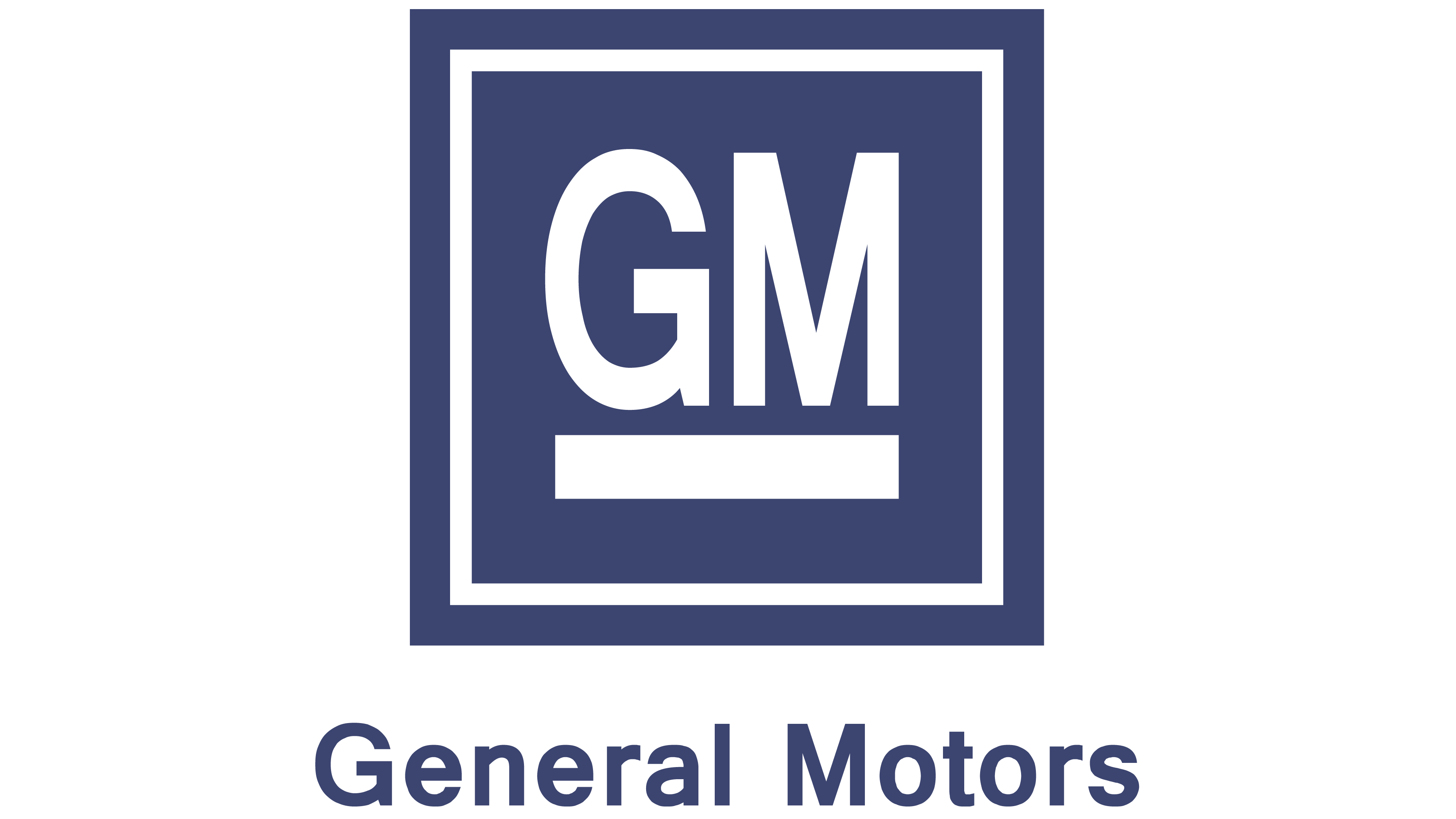
General Motors Logo LogoDix
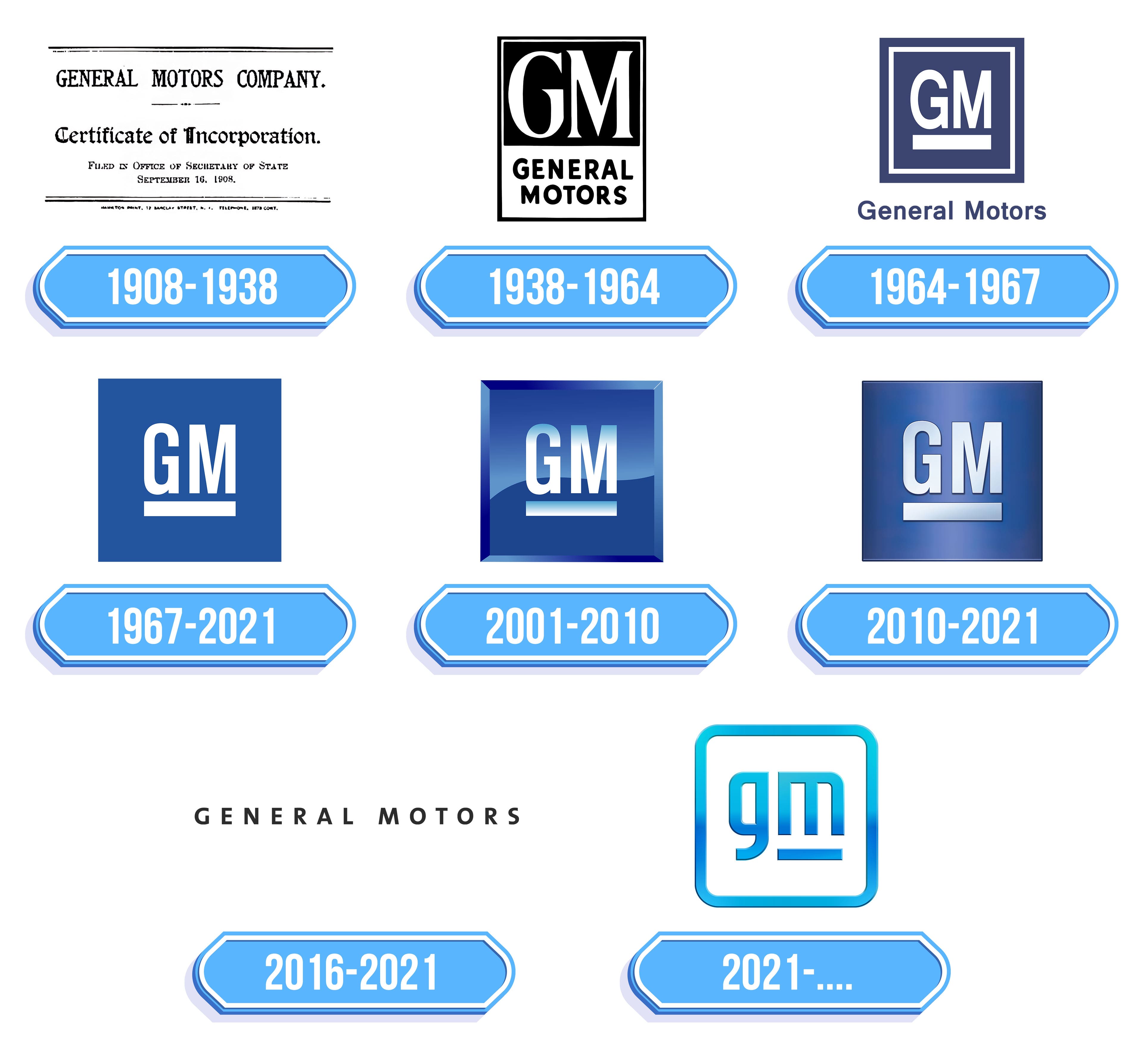
General Motors Logo Storia e significato dell'emblema del marchio
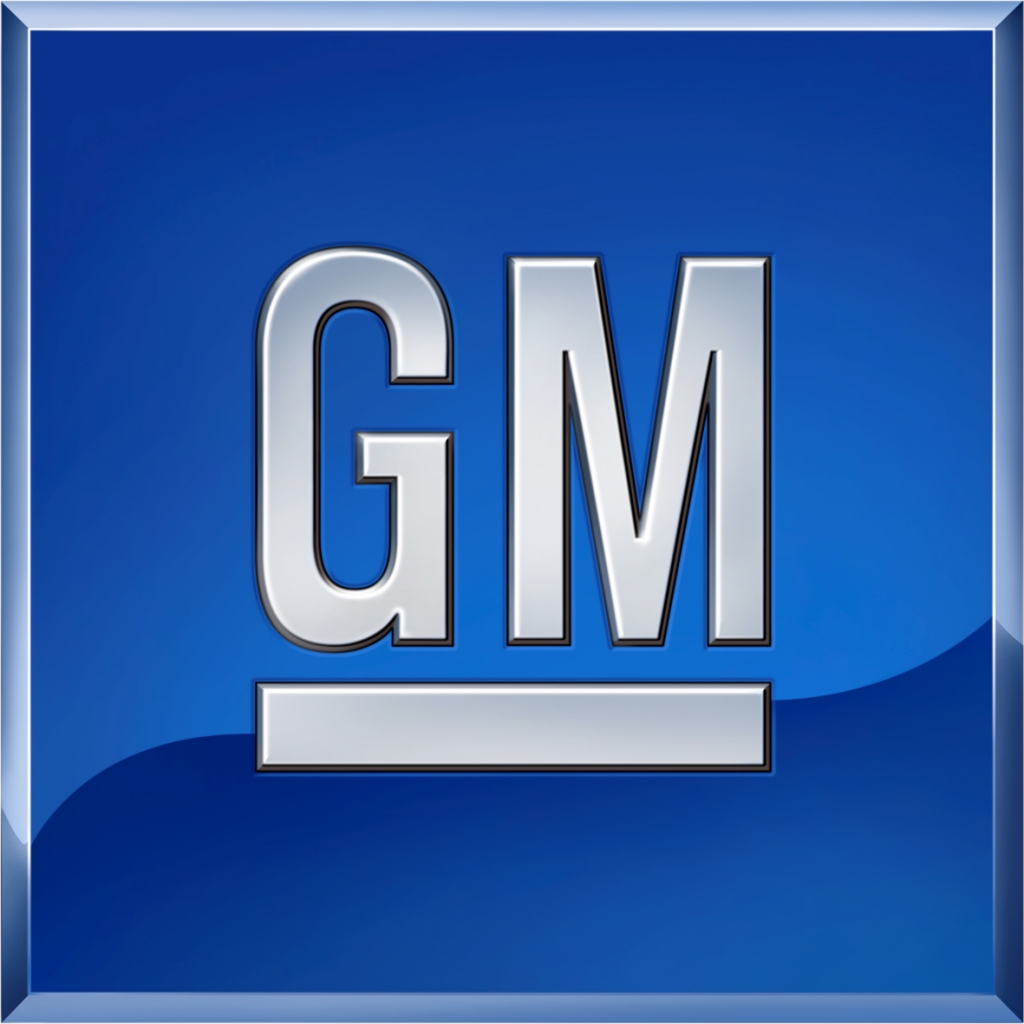
General Motors Logo / Automobiles / Logonoid